A roughing pump is a type of vacuum pump that is used to create a rough or preliminary vacuum in a system. A good vacuum specification for a roughing pump would depend on the specific application and requirements of the system. However, generally speaking, a roughing pump should be able to achieve a vacuum level of at least 1 x 10^-3 Torr. This is sufficient for most applications requiring a rough vacuum. Additionally, the pumping speed and ultimate vacuum of the pump will also be important factors to consider. It is always a good idea to consult with the pump manufacturer or a vacuum systems expert to determine the best vacuum specification for a specific application.
Choosing the right vacuum pump for your application can be a daunting task, as there are many different types and models available on the market. In this article, we will discuss the key factors to consider when selecting a vacuum pump and provide some guidelines to help you make an informed decision.
- Application
The first step in choosing a vacuum pump is to determine the specific application for which it will be used. Different types of pumps are designed for different purposes, such as roughing, high-vacuum, or ultra-high vacuum. This will help you narrow down your options and select a pump that is best suited for your needs.
- Vacuum Level
The vacuum level is the measure of the pressure inside the system, and it is measured in units such as Torr or Pascals. Different pumps are capable of achieving different vacuum levels, so it is important to determine the required vacuum level for your application and select a pump that can achieve that level.
- Flow Rate
The flow rate is the amount of gas or air that the pump can move in a given time period. It is measured in units such as cubic feet per minute (CFM) or liters per second (L/s). The flow rate will depend on the size of the system, the number of leaks, and the required pumping speed. A pump with a higher flow rate will be able to pump the system faster than one with a lower flow rate.
- Ultimate Vacuum
The ultimate vacuum is the lowest pressure that the pump can achieve, and it is measured in units such as Torr or Pascals. This is an important factor to consider, as some applications require a very low vacuum level.
- Pumping Speed
Pumping speed is the rate at which the pump can evacuate the system, and it is measured in units such as liters per second (L/s) or cubic feet per minute (CFM). This will depend on the size of the system, the number of leaks, and the required pumping speed. A pump with a higher pumping speed will be able to evacuate the system faster than one with a lower pumping speed.
- Cost
Cost is also an important factor to consider when choosing a vacuum pump. Some pumps are more expensive than others, and the cost will depend on the type of pump, its capabilities, and the manufacturer.
- Maintenance
Maintenance is also an important factor to consider when choosing a vacuum pump. Some pumps require more maintenance than others, and this can depend on the type of pump, its capabilities, and the manufacturer.
- Brand and Quality
It is always a good idea to select a vacuum pump from a reputable brand, as these pumps are typically of higher quality and have a better track record of performance. Additionally, it is also good to look for pumps that are built with high-quality materials, such as stainless steel, as these pumps will last longer and be less likely to experience problems.
By considering these factors, you can choose a vacuum pump that is best suited for your specific application and requirements. It is always a good idea to consult with the pump manufacturer or a vacuum systems expert to determine the best vacuum specification for a specific application.
What are the main types of vacuum pumps?
Vacuum pumps are devices that are used to remove gas molecules from a sealed chamber or system in order to create a vacuum. There are several different types of vacuum pumps available on the market, each with its own specific capabilities and characteristics. In this article, we will discuss the main types of vacuum pumps and explain the differences between them.
- Positive Displacement Pumps
Positive displacement pumps are the most common type of vacuum pump and are used in a wide range of applications. They work by trapping a fixed volume of gas and then compressing it to a smaller volume, which results in a reduction of pressure. Positive displacement pumps can be further divided into two main types: rotary and reciprocating.
- Rotary pumps: Rotary pumps use a rotating mechanism, such as a rotor or a screw, to compress the gas. They are typically used in applications that require a low to medium vacuum level and have a relatively high pumping speed.
- Reciprocating pumps: Reciprocating pumps use a piston or diaphragm to compress the gas. They are typically used in applications that require a medium to high vacuum level and have a relatively low pumping speed.
- Kinetic Pumps
Kinetic pumps are a type of vacuum pump that uses kinetic energy to remove gas molecules from a sealed chamber or system. They work by increasing the speed of the gas molecules, which causes them to collide with the walls of the pump and be removed from the system. Kinetic pumps can be further divided into two main types: turbomolecular and diffusion.
- Turbomolecular pumps: Turbomolecular pumps use a series of rotating blades to increase the speed of the gas molecules. They are typically used in applications that require a high vacuum level and have a relatively high pumping speed.
- Diffusion pumps: Diffusion pumps use a jet of high-speed gas to increase the speed of the gas molecules. They are typically used in applications that require a very high vacuum level and have a relatively low pumping speed.
- Sorption Pumps
Sorption pumps are a type of vacuum pump that uses a material to adsorb or trap gas molecules. They work by using a material such as charcoal or zeolite, which adsorbs the gas molecules and holds them in place. Sorption pumps are typically used in applications that require a very high vacuum level and have a relatively low pumping speed.
- Cryogenic Pumps
Cryogenic pumps are a type of vacuum pump that uses low temperatures to remove gas molecules from a sealed chamber or system. They work by cooling the gas molecules to a temperature below their boiling point, which causes them to condense and be removed from the system. Cryogenic pumps are typically used in applications that require a very high vacuum level and have a relatively low pumping speed.
In conclusion, there are several different types of vacuum pumps available on the market, each with their own specific capabilities and characteristics. Positive displacement pumps are the most common type of vacuum pump and are used in a wide range of applications. Kinetic pumps, Sorption pumps and Cryogenic pumps are also used in specific applications where high vacuum level is required. The choice of the right vacuum pump will depend on the specific application and requirements of the system. It is always a good idea to consult with the pump manufacturer or a vacuum systems expert to determine the best vacuum pump for a specific application.
When should you use a rotary vane vacuum pump?
A rotary vane vacuum pump is a type of positive displacement vacuum pump that uses a rotor with sliding vanes to compress and remove gases from a sealed chamber or system. They are commonly used in industrial, laboratory and research applications. They are a good choice in following cases:
- Low to medium vacuum level: Rotary vane pumps are capable of achieving vacuum levels between 1 x 10^-3 to 1 x 10^-1 Torr. They are typically used in applications that require a low to medium vacuum level, such as laboratory experimentation, packaging, and vacuum forming.
- High pumping speed: Rotary vane pumps have a relatively high pumping speed, which makes them a good choice for applications that require a fast evacuation of the system. They can pump large volumes of gas in a short amount of time.
- Continuous operation: Rotary vane pumps are designed for continuous operation, which makes them a good choice for applications that require a continuous supply of vacuum.
- Chemical and Pharmaceutical Applications: Rotary vane pumps are suitable for applications that require chemical and pharmaceutical environments as they are resistant to most gases and chemicals.
- Low maintenance: Rotary vane pumps are relatively low maintenance and do not require frequent oil changes or other maintenance tasks.
It is important to note that rotary vane pumps are not suitable for applications that require a high vacuum level, as they can only achieve a vacuum level of around 1 x 10^-1 Torr. In such cases, Kinetic pumps or Sorption pumps are more appropriate. Additionally, it’s always a good idea to consult with the pump manufacturer or a vacuum systems expert to determine the best vacuum pump for a specific application.
When should you use a diaphragm vacuum pump?
A diaphragm vacuum pump is a type of positive displacement vacuum pump that uses a flexible diaphragm to compress and remove gases from a sealed chamber or system. They are commonly used in laboratory, industrial and research applications. They are a good choice in following cases:
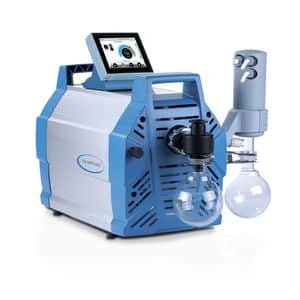
- Medium to high vacuum level: Diaphragm pumps are capable of achieving vacuum levels between 1 x 10^-3 to 1 x 10^-5 Torr. They are typically used in applications that require a medium to high vacuum level, such as laboratory experimentation, packaging, and vacuum forming.
- Low flow rate: Diaphragm pumps have a relatively low flow rate, which makes them a good choice for applications that do not require a high pumping speed. They are well suited for applications where a low flow rate is sufficient to achieve the desired vacuum level.
- Chemical and Pharmaceutical Applications: Diaphragm pumps are suitable for applications that require chemical and pharmaceutical environments as they are resistant to most gases and chemicals.
- Low maintenance: Diaphragm pumps are relatively low maintenance and do not require frequent oil changes or other maintenance tasks.
- Pumps for aggressive and corrosive gases: Diaphragm pumps are ideal for applications that require pumping of aggressive and corrosive gases as the diaphragm isolates the gases from the moving parts of the pump.
It is important to note that diaphragm pumps are not suitable for applications that require a high pumping speed, as they have a relatively low flow rate. Additionally, diaphragm pumps are not suitable for applications that require a very high vacuum level, as they can only achieve a vacuum level of around 1 x 10^-5 Torr. In such cases, Kinetic pumps or Sorption pumps are more appropriate. As always, it’s always a good idea to consult with the pump manufacturer or a vacuum systems expert to determine the best vacuum pump for a specific application.
When should you use a liquid ring vacuum pump?
A liquid ring vacuum pump is a type of positive displacement vacuum pump that uses a rotating impeller within a cylindrical chamber that is partially filled with liquid. The impeller creates a liquid ring that compresses and removes gases from a sealed chamber or system. They are commonly used in industrial and process applications. They are a good choice in following cases:
- Low to medium vacuum level: Liquid ring pumps are capable of achieving vacuum levels between 1 x 10^-3 to 1 x 10^-2 Torr. They are typically used in applications that require a low to medium vacuum level, such as chemical processing, paper manufacturing, and power generation.
- Handling of liquids and humid gases: Liquid ring pumps are ideal for applications where the pumped gas contains liquids or water vapor, as the liquid ring created by the impeller helps to condense and remove the liquid from the gas.
- Continuous operation: Liquid ring pumps are designed for continuous operation and are well suited for applications that require a continuous supply of vacuum.
- Handling of corrosive and abrasive gases: Liquid ring pumps are suitable for applications that require pumping of corrosive and abrasive gases as the liquid ring created by the impeller provides a barrier between the gases and the moving parts of the pump.
- Low maintenance: Liquid ring pumps are relatively low maintenance and do not require frequent oil changes or other maintenance tasks.
It is important to note that liquid ring pumps are not suitable for applications that require a high vacuum level, as they can only achieve a vacuum level of around 1 x 10^-2 Torr. In such cases, Kinetic pumps or Sorption pumps are more appropriate. Additionally, liquid ring pumps are not well suited for applications that require a high pumping speed, as they have a relatively low flow rate. As always, it’s always a good idea to consult with the pump manufacturer or a vacuum systems expert to determine the best vacuum pump for a specific application.
When should you use a scroll vacuum pump?
A scroll vacuum pump is a type of positive displacement vacuum pump that uses a fixed and a moving spiral-shaped element (scroll) to compress and remove gases from a sealed chamber or system. They are commonly used in laboratory, industrial and research applications. They are a good choice in following cases:
- Medium to high vacuum level: Scroll pumps are capable of achieving vacuum levels between 1 x 10^-3 to 1 x 10^-5 Torr. They are typically used in applications that require a medium to high vacuum level, such as laboratory experimentation, packaging, and vacuum forming.
- Low noise operation: Scroll pumps are known for their low noise operation which makes them a good choice for applications that require a quiet operation.
- Low vibration: Scroll pumps are known for their low vibration operation which makes them a good choice for applications that require a low vibration operation.
- High pumping speed: Scroll pumps have a relatively high pumping speed, which makes them a good choice for applications that require a fast evacuation of the system. They can pump large volumes of gas in a short amount of time.
- Low maintenance: Scroll pumps are relatively low maintenance and do not require frequent oil changes or other maintenance tasks.
It is important to note that scroll pumps are not suitable for applications that require a very high vacuum level, as they can only achieve a vacuum level of around 1 x 10^-5 Torr. In such cases, Kinetic pumps or Sorption pumps are more appropriate. Additionally, Scroll pumps are not suitable for applications that require pumping of corrosive and abrasive gases, as they are not able to handle those types of gases. As always, it’s always a good idea to consult with the pump manufacturer or a vacuum systems expert to determine the best vacuum pump for a specific application.
When should you use a turbomolecular vacuum pump?
A turbomolecular vacuum pump is a type of kinetic vacuum pump that uses a series of rotating blades to increase the speed of the gas molecules, which causes them to collide with the walls of the pump and be removed from the system. They are commonly used in industrial, laboratory and research applications. They are a good choice in following cases:
- High vacuum level: Turbomolecular pumps are capable of achieving vacuum levels as low as 1 x 10^-10 Torr and are typically used in applications that require a high vacuum level, such as semiconductor manufacturing, scientific research, and vacuum coating.
- High pumping speed: Turbomolecular pumps have a relatively high pumping speed, which makes them a good choice for applications that require a fast evacuation of the system. They can pump large volumes of gas in a short amount of time.
- High ultimate vacuum: Turbomolecular pumps are capable of reaching high ultimate vacuum levels, making them suitable for applications that require a very high vacuum level.
- High compression ratio: Turbomolecular pumps have a high compression ratio, which makes them a good choice for applications that require a high compression ratio.
- Low maintenance: Turbomolecular pumps are relatively low maintenance and do not require frequent oil changes or other maintenance tasks.
It is important to note that turbomolecular pumps are not suitable for applications that require the pumping of corrosive and abrasive gases, as they are not able to handle those types of gases. Additionally, turbomolecular pumps are more expensive than other types of vacuum pumps and are not ideal for applications that do not require a high vacuum level. As always, it’s always a good idea to consult with the pump manufacturer or a vacuum systems expert to determine the best vacuum pump for a specific application.
How to choose between a vacuum pump without oil and a lubricated vacuum pump?
- Application: The specific application for which the vacuum pump will be used is an important factor to consider when choosing between an oil-free and lubricated vacuum pump. Oil-free pumps are ideal for applications that require a clean and oil-free environment, such as semiconductor manufacturing and food processing. Lubricated pumps, on the other hand, are suitable for applications that do not have strict requirements for a clean and oil-free environment.
- Vacuum level: The vacuum level required for the application is another important factor to consider. Oil-free pumps can typically achieve a lower vacuum level than lubricated pumps, making them suitable for applications that require a very high vacuum level.
- Maintenance: Lubricated vacuum pumps require regular oil changes and maintenance to ensure proper operation, while oil-free pumps do not require oil changes and have less maintenance.
- Cost: Oil-free pumps are generally more expensive than lubricated pumps due to the complexity of their design and the materials used in their construction.
- Efficiency: Lubricated vacuum pumps tend to be more efficient in terms of pumping speed and ultimate vacuum than oil-free pumps, because lubricated pumps are cooled by the oil, which helps to reduce the temperature of the moving parts and increase the efficiency of the pump.
- Noise: Oil-free pumps tend to be quieter than lubricated pumps because they don’t have the noise associated with the oil.
It is important to note that oil-free pumps are not suitable for every application and lubricated pumps are not always the best choice as well. It’s always a good idea to consult with the pump manufacturer or a vacuum systems expert to determine the best vacuum pump for a specific application. Additionally, it’s also important to consider other factors like the size, weight, and portability of the pump. For example, if the pump needs to be moved frequently, an oil-free pump may be a better choice because it is generally smaller and lighter than a lubricated pump.
Another important aspect to consider is the operating temperature range. Lubricated pumps have a wider operating temperature range compared to oil-free pumps, which can be beneficial for applications that require the pump to operate in extreme temperatures.
Lastly, it’s also important to consider the environment in which the pump will be operated. Oil-free pumps are better suited for cleanroom environments and applications that require a low particulate and oil-free environment. Lubricated pumps, on the other hand, can be used in environments where oil leaks or spills are acceptable.
In summary, when choosing between an oil-free and lubricated vacuum pump, it’s important to consider factors such as the specific application, vacuum level required, maintenance, cost, efficiency, noise, and the operating temperature range, as well as the environment in which the pump will be operated. Consultation with the pump manufacturer or a vacuum systems expert can provide you with more detailed information and help you make the best choice for your specific application.
What are the main uses of vacuum pumps?
Vacuum pumps are used in a wide range of applications across different industries, some of the main uses include:
- Industrial processes: Vacuum pumps are used in many industrial processes such as chemical processing, power generation, and paper manufacturing to create a vacuum and control the pressure in sealed chambers or systems.
- Semiconductor manufacturing: Vacuum pumps are used in the production of semiconductors to create a high vacuum environment, which is necessary for the growth of thin films and other processes.
- Laboratory research: Vacuum pumps are used in scientific research and experimentation to create a high vacuum environment, which is necessary for certain types of measurements and experiments.
- Packaging and vacuum forming: Vacuum pumps are used in the packaging industry to remove air from sealed containers, such as food packaging and vacuum forming of plastics.
- Medical and dental equipment: Vacuum pumps are used in medical and dental equipment such as suction devices and vacuum-assisted surgical instruments.
- Automotive industry: Vacuum pumps are used in automotive industry for brake systems, air conditioning, power steering and other systems that require vacuum.
- Environmental and Energy: Vacuum pumps are used in environmental and energy industry for example in solar panel manufacturing, and in the production of biofuels.
- Aerospace and Military: Vacuum pumps are used in aerospace and military industry for example in the manufacturing of aircraft, spacecraft and missile systems.
These are just a few examples of the many different types of applications that vacuum pumps are used in. The choice of the right vacuum pump will depend on the specific application and requirements of the system. It is always a good idea to consult with the pump manufacturer or a vacuum systems expert to determine the best vacuum pump for a specific application.