When processing metals with a high melting point, you’ll need an appropriate process for effectively processing your metals. The cold chamber pressure die casting process is essential as it helps produce mass products with smooth and quality surfaces. You’ll use various metal alloys such as brass, aluminum, zinc, and copper alloys to create top-quality products during the process.
Apart from being effective, helping in processing metal with a high melting point, and being a budget-friendly process, this process has numerous benefits. Read through the article to understand the top benefits of this metal process.
- Multiple finishing techniques
When dealing with different metals with high melting points, most of the process usually doesn’t achieve the best finishes. However, with the proper components and procedures of the cold chamber pressure die casting process, you’ll get well-textured, smooth, and high-quality products from the process. It also offers an effortless finishing technique as these metal parts will only require minimal preparations. Most manufacturers use this process to have mass production of identical products with top features.
- High production speed
The speed of production is essential in any metal processes in particular companies or industries. Compared to the hot chamber die casting, this method produces various shapes and designs quickly. Additionally, to achieve mass production in a short span, you’ll require little to no machines. The process is essential to help individuals achieve a lot of products with identical casting. Remember, the faster production rate doesn’t compromise the product’s quality, as you’ll have mass production of quality products.
- Increase of strength and weight
Some researchers carried out a study to determine the strength of products from the plastic molding and the cold chamber pressure die casting. The results were clear that the products from this process have more strength and weight than the plastic injections molding products. Despite having similar dimensions and using the same raw products, they found that the products from this process were heavier and stronger. The process produces the perfect products for most industries that require strong and long-lasting thin-wall castings.
- Dimensional accuracy and stability
When looking for metals with prime and durability components, it’ll be essential to consider the metal precision products from this process. The process provides high-quality metal parts with dimensional stability and accuracy. You can use these products in any environment despite the adverse conditions of the place or process. These casting products usually have high tolerance, durability, and heat resistance properties. Additionally, using these products from your projects reduces the maintenance cost, as they require minimal maintenance throughout the project.
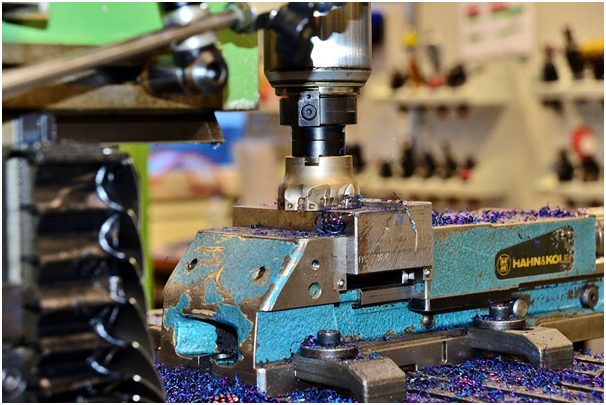
Wrapping it up
When a particular project requires processing metals with high melting points for its activities, it may be challenging to find a suitable metal processing method. However, it’ll be essential to choose the cold chamber pressure die casting process for your metal processing. This method has numerous benefits, including mass production of quality products and providing dimensional accuracy and stability. Lastly, the method is an effective process that’ll help you get the most durable products resistant to adverse conditions.